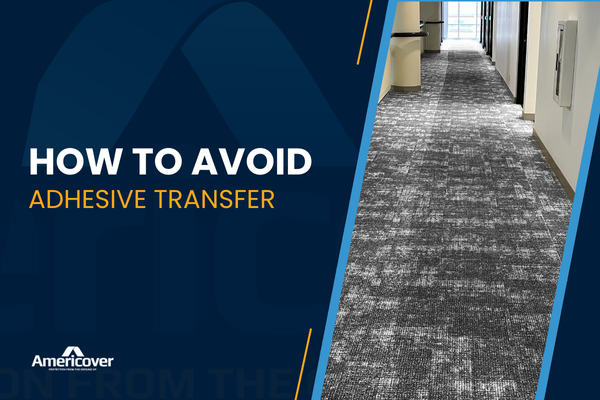
What You Need to Know About Carpet Protection Adhesives, Film Thickness, and Environmental Factors
Have you ever dealt with adhesive transfer from a carpet protection product you’ve used? If so, you’re not alone. One of our recent customers came to us looking for help—not because they had purchased our product, but because they used a competitor’s and were struggling to remove adhesive residue. Their experience highlights how important it is to understand what makes carpet protection effective—and what factors can lead to failure.
In this blog, we’ll walk through the pros and cons of self-adhesive carpet protection films, what to consider when selecting a product, how application time and environment impact performance, and tips to help you get the most out of your floor protection investment.
The Pros and Cons of Self-Adhesive Carpet Protection Film
Self-adhesive films are a convenient and effective option for short-term carpet protection. They’re commonly used in construction, remodeling, moving, or events—anywhere foot traffic and jobsite activity could damage the flooring.
Pros:
- Fast and easy to install
- No tape or fasteners required
- Provides a slip-resistant walking surface
- Clean, professional appearance
Cons:
- Must be removed within the recommended timeframe (usually 30–45 days)
- Can leave adhesive residue if left too long
- Performance can vary depending on film thickness and carpet type
How Adhesive Type and Film Thickness Affect Performance
Two major factors influence how a carpet protection film performs: the type of adhesive and the thickness of the film.
Film Thickness Matters Most carpet protection films on the market range from 2 mil to 4 mil thick. Thinner films (2 mil) are typically more budget-friendly and flexible, making them easier to install on low-pile carpets in light-duty applications. However, they may be more prone to tearing, especially in high-traffic or heavy-use environments.
Heavier-duty options like Americover’s 3 mil films strike a balance between flexibility and strength. At this thickness, the film is more puncture- and tear-resistant, ideal for construction sites, remodeling projects, or any area exposed to tools, ladders, or equipment.
Not All Adhesives Are Created Equal Carpet protection films typically use one of the following adhesive types:
- Water-Based Adhesive: Known for its clean removal, this type of adhesive is less likely to cause discoloration or dye transfer on carpets. It’s pressure-sensitive and safe for synthetic carpet fibers, making it a reliable choice for professional use—as seen in Americover’s Carpet Cover and Fire Retardant Carpet Cover films.
- Solvent-Based Adhesive: Often used in lower-cost or imported films, solvent-based adhesives can be more aggressive. While they may stick well initially, they have a higher risk of leaving residue—especially if the film is left down too long or exposed to heat. These adhesives may also interact poorly with carpet dyes and finishes.
- Rubber-Based Adhesive: This type offers strong tack and adhesion, but like solvent-based adhesives, can be harder to remove cleanly, particularly from plush or high-pile carpets. It’s more commonly used in industrial applications, where surface finish is less of a concern.
Adhesive Shelf Life and Degradation: Why Age Matters
Even the best adhesive won’t perform well if the product is past its prime. Like paint or caulk, carpet protection films have a shelf life, and over time, the adhesive can begin to degrade—even if the roll has never been opened.
What Happens When Adhesive Degrades?
- Loss of tack – The adhesive may not stick properly to carpeted surfaces, especially in corners or around edges.
- Uneven adhesion – Part of the film sticks too aggressively while other areas lift or shift.
- Higher risk of residue – Older adhesive is more likely to transfer to carpet fibers.
- Film separation – Degraded adhesive can cause delamination, making removal more difficult or damaging.
How to Avoid Adhesive Failures
- Check production or expiration dates if available.
- Store rolls upright in a cool, dry place.
- Use older stock first.
- Avoid using leftover film stored in hot or humid conditions.
Environmental Factors That Impact Performance
- Never install adhesive carpet protection on wet or damp carpet.
- Never install adhesive carpet protection over glue-down carpet for a minimum of 72 hours to allow the glue to “breathe.”
- If carpet has been installed over a newly poured cement slab that is not fully cured, avoid using adhesive carpet protection as it can trap the cement moisture and discolor the carpet.
- In cases of extreme heat, shorten the recommended application time by 50%.
Best Practices for Installation
- Start with a clean, dry carpet.
- Apply in manageable sections using even pressure.
- Avoid stretching or over-tacking the film.
- Label the roll or project area with the installation date.
- Remove the film within 30–45 days depending on product guidelines and site conditions.
Tips for Removing Adhesive Residue
Water-based adhesive film residue easily removes with warm water and can be quickly removed via steam cleaning. Using a 180˚F head temperature on the steam cleaner will rehydrate the adhesive and cause it to ball up and lift cleanly.
Citrus-based cleaners (available at most hardware stores) may help remove solvent-based adhesive residue. If further problems persist, contact your local surface protection supplier.
Carpet discoloration is often caused by trapped moisture beneath the film, which results in a chemical reaction with the carpet fibers. Unfortunately, this type of damage may only be resolved by replacing the affected area.
Product Recommendations
Self-Adhesive Carpet Protection Films:
Non-Adhesive, Reusable Carpet Protection:
Reusable solutions may cost more up front, but they offer long-term savings through durability, multiple uses, and zero risk of adhesive transfer.
Need Help Choosing the Right Product? Live chat with our experts to find the best solution for your application.