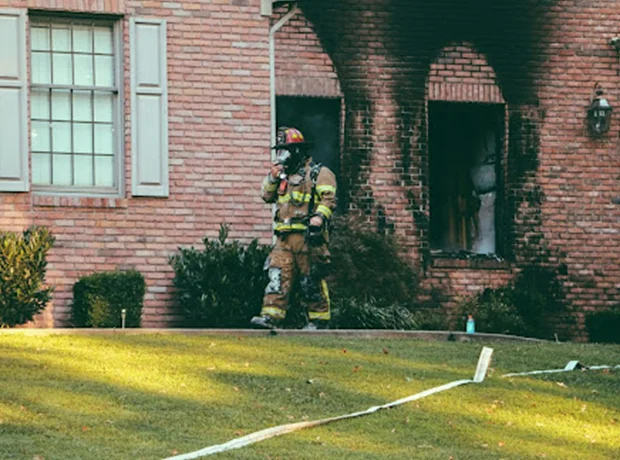
Electrical hazards account for a large percentage of jobsite accidents and worker fatalities. According to a report from the Center for Construction Research and Training (CPWR), between 1992 and 2008, nearly half of all construction fatalities in the U.S. occurred as a result of electrocution on the job site.
While the statistics are grim, proper training and awareness programs are helping to reduce these numbers and improve construction safety. But we can do better.
In recognition of National Electrical Safety Month, we are highlighting some of the common electrical hazards that can be found around the jobsite as well as precautions you can take to reduce the risk of electrocution and electrical fires.
1. Overhead Power Lines
According to the Electrical Safety Foundation International (ESFI), from 2011 to 2017, 36 percent of all electricity-related workplace fatalities were caused by overhead power lines. The first and most important step to avoiding these dangers is to look up and around to locate all of the powerlines on and surrounding the job site. Once you know where the power lines are, adhering to a strict set of safety measures can help protect you and your team from serious injury and death.[/vc_column_text]
ESFI outlines the following powerline safety steps to avoid electrocution from power lines:
- Always locate all overhead power lines on or near the jobsite.
- Keep yourself and all equipment at least 10 feet away from all overhead power lines.
- Do not touch anything that is in contact with a powerline.
- Be aware of fencing near power lines.
- Carry ladders and other equipment horizontally. Be careful with rolling scaffolds.
- Lower equipment apparatus prior to driving near power lines.
- Never spray water near power lines.
- Stay at least 35 feet away from a fallen powerline.
For more ESFI overhead power line safety tips, visit www.esfi.org/overhead-power-line-safety.
2. Damaged Equipment and Cords
Exposure to damaged electrical tools, equipment, and cords can be fatal.
On the construction site, damaged electrical tools and equipment can be more than just an annoyance – they can be fatal. Something as seemingly minor as an exposed wire or frayed cable can cause a spark, posing both an electrocution and fire hazard.
To mitigate this risk, every construction site should have a designated person in charge of ensuring all electrical tools, switches, cables and cords are functioning safely by examining them frequently and thoroughly for cracks, cuts or abrasions. If a cord is found to be damaged, either replace it immediately or have it repaired by someone who is qualified to do so. To prevent cord damage from happening in the first place, be sure to always protect cords and cables from sharp corners and objects.
Unsure whether an extension cord can be repaired and reused? See OSHA’s Standard Interpretation here.
Extension cords must always have grounding plugs (i.e., no multiple plug adaptors), and all electrical tools must be properly grounded unless they are double insulated.
If you are using an electric hand tool and it breaks, OSHA requires it be restored to its “approved condition” to prevent electrical hazards. Cord sets used with portable electric tools should be three-wire type and designed for hard or extra-hard service.
Having a lockout/tagout procedure in place is critical to mitigating the risk of electrical hazards on the job site. OSHA defines lockout/tagout as a means of protecting workers from electrocution stemming from “the unexpected energization or startup of machinery and equipment, or the release of hazardous energy during service or maintenance activities.”
Again, a designated person should ensure that all equipment in question is properly shut off, disconnected from the electrical source, locked and/or tagged to prevent injury resulting from the unexpected release of electricity. In fact, US Federal Regulation 29 CFR 1910.147 (c) (5) (ii) (c) (1) states that “the tag must have an identification showing the name of the person doing the lock and tag.”
3. Inadequate Wiring, Overloaded Circuits, and Improper Grounding
Electrocution risks are myriad, from burn and shock hazards to arc flashes, blasts, fires and explosions. These hazards can be caused by a variety of factors, including, but not limited to:
1. Faulty wiring
2. Improper cord use
3. No Ground-Fault Circuit Interrupter (GFCI) outlets in wet conditions
4. Reversed polarity
5. Lack of an assured grounding conductor program
To prevent overheating and resulting fire hazards, it is important to ensure you are using the right wire size and not overloading your outlets. Also, be sure to check all circuit breakers to make sure they are functioning properly (i.e., cutting the power until the issue is remedied).
Here are some best practices you can follow to ensure your wires, circuits and grounding techniques are safe and adequate:
- Perform regular fire risk assessments to identify areas at risk of bad wiring and circuits
- Keep temporary extension wiring to a minimum and ensure they’re not overloading existing circuits
- Keep the use of portable lamps to a minimum and ensure the ones in use have appropriate guards
- Keep main switches of all electrical circuits in the “off” position when equipment is not in use
- Ensure fire equipment is easily accessible and well maintained
- Maintain proper grounding to eliminate unwanted voltage and reduce the risk of electrocution
- For temporary power sources, always use a GFCI for portable cords or an assured equipment grounding conductor program
- Verify that all wiring is coming from a properly rated circuit and doesn’t exceed capacity
4. Operating Electrical Equipment in Wet Conditions
Water and electricity generally do not mix – especially if the equipment’s insulation is damaged. In the rain-or-shine world of construction, safety precautions must be taken to prevent the risk of electrocution in wet environments.
If you must operate electrical equipment in wet conditions, be sure you are using OSHA-compliant products that satisfy current safety requirements. Here are a few key measures you can take to stay safe when handling machinery near water:
- If equipment gets wet, have a qualified electrician inspect the equipment prior to re-energizing it
- Use a GFCI for portable cords
- Wear the right gear, including:
- Clothing made from flame-resistant/retardant materials
- Leather work boots
- Gloves insulated with rubber
- Safety glasses
- Use watertight wiring devices (plugs, connectors, inlets, outlets and FD boxes) and corrosion-resistant devices (connectors and receptacles) designed for harsh wet and damp locations
- Employ best practices for personal safety by:
- Making sure the hand tools you’re using are insulated
- Keeping metal off your person, including car keys, jewelry and watches, as these can all conduct electricity
5. Failing to Use Fire-Retardant Materials
Using materials that are not suitable for a specific construction environment can contribute to the risk of fire hazards on the job site.
Related Article: What is Fire Retardant Anti-Static Plastic Sheeting?
The Role of Fire-Retardant Plastic Sheeting
If you are performing construction in a data center, hospital, museum or any other area where a single spark could result in a deadly fire, building codes require you to use NFPA 701 and ASTM E84 tested fire-retardant and/or antistatic plastic sheeting. These materials can potentially reduce property damage and save lives.
Fire-retardant plastic sheeting is specially designed to slow the spread of a fire, unlike regular poly sheeting, which burns rapidly when exposed to flames. While fire-retardant plastic sheeting does not necessarily mean fireproof, the additives in the plastic allow for the sheeting to self-extinguish, which interrupts the natural combustion process and reduces the plastic’s ability to act as a significant fuel source for the fire.
Reducing Electrostatic Discharge With Anti-static Sheeting
Anti-static plastic sheeting is another important safety element to incorporate into your construction projects. It functions by minimizing sparks from static electricity, which are a common cause of building fires.
Generally speaking, most plastics are excellent insulators, meaning they conduct electricity quite poorly. However, as a result of this, electrical charges can accumulate on their surface, leading to static build-up. This usually happens when materials slide or rub against each other, resulting in static discharge when the plastic comes into contact with a person or an electronic device. Anti-static plastic dissipates static buildup faster than normal plastic sheeting would, not only protecting equipment from damage, but also ensuring more fire safety overall.
Fire Ratings for Plastic Sheeting
Plastic sheeting comes in a variety of fire safety ratings that can range in price depending on the protection levels they provide. Here’s a closer look at the main ratings you’ll find for fire-retardant plastic sheeting:
NFPA 701
NFPA 701 is the most common of plastic sheeting fire safety certifications, and mainly focuses on the flame propagation of textiles and films. The goal is that products that pass this certification will have a much smaller flame propagation than typical plastics.
UL 214
UL 214 tests the performance in flame-exposure tests of flame-resistant fabrics. If your sheeting is able to catch fire quicker than the parameters of the certification, it will not be accepted.
ASTM E-84
The ASTM E-84 certification tests how flames spread across the surface of a material, along with the level of smoke it produces. If above a certain threshold, the sheeting will not be certified.
CPAI 84
CPAI 84 is a risk of flammability rating created for recreational materials. Its certification means that your product is rated to have the same flame resistance of fabric used in manufacturing camping tents.
Recommended Product for Electrical and Fire Safety
For more than 25 years, Americover has been supplying contractors with specialty plastic sheeting products that meet all relevant industry standards. The following products are recommended for construction projects that require fire-retardant materials.
Product Links:
ASFR6
ASFR6 is ideal for use in hospitals, healthcare environments, data centers and anywhere you need to protect electrical equipment or create an antistatic dust barrier.
Fire Retardant Tape
This multi-purpose tape has a high tack but can be repositioned and it removes cleanly from many surfaces. It is ideal for seaming, sealing, and repairing flame retardant plastic sheeting materials during remodel and remediation applications in environments that require flame retardant materials.
4-Mil White Fire-Retardant Plastic Sheeting
4-Mil White Fire-Retardant Plastic Sheeting is a cost-effective solution that creates excellent protection across a variety of applications, including construction sites, theaters, movie sets and more. Fire certificates are included with every purchase.
Black Fire-Retardant Plastic Sheeting
Black Fire-Retardant Plastic Sheeting contains fire-retardant additives and UV inhibitors that extend the service life of the poly and ensure compliance with NFPA 701 Test 1, ASTM E-84 and California Title 19 fire safety regulations.
Hard Surface Cover FR
Hard Surface Cover FR is a fire-retardant, anti-slip embossed polyolefin film certified for NFPA 701 Test 1, GSA standard 191 methods, 5903 fire test and other government standards for fire safety. This reusable film provides medium- to heavy-duty protection on construction sites and is suitable for both short and long-term protection of floors, decks, courts, corridors and more.
Self-Adhesive Carpet Cover (available in fire-retardant)
Self-Adhesive Carpet Cover is a versatile and high-quality clear specialty film that provides reliable protection for any carpeted surface. Contractors prefer Americover’s carpet cover because of its strength, quality and outstanding on-the-job performance.
Dura-Skrim® Fire-Retardant Reinforced Plastic Sheeting
Dura-Skrim Fire-Retardant Reinforced Plastic Sheeting is a puncture-resistant construction film reinforced with a layer of polyester scrim to prevent tearing. Dura-Skrim from Americover is imprinted with the words “Fire-retardant.”
Tuff Scrim™ Antistatic Fire-Retardant Reinforced Poly Sheeting
Tuff Scrim Antistatic Fire-Retardant Reinforced Poly Sheeting is a reinforced laminate film engineered with fire-retardant and antistatic additives. It passes NFPA 701 Large Scale requirements and has a Class I/Class A flame spread rating per UBC-42 and ASTM E-84.
Tuff-Scrim™ Fire-Retardant Reinforced Poly Sheeting
Tuff-Scrim Fire-Retardant Reinforced Poly Sheeting is a heavy-duty, lightweight material that won’t rip or tear. Tuff-Scrim passes NFPA 701 Large Scale requirements for Standard Methods of Fire Tests for Flame-Resistant Textiles and Films, and most options have a Class I/Class A Flame Spread rating per UBC-42 and ASTM E-84. Fire certificates are included with every purchase.
Fire-retardant Correx® Boards
Fire-retardant Correx Boards are a lightweight, reusable and cost-effective solution to protect floors and surfaces during construction projects.
Need fire-retardant duct tape or electrical tape? Shop our selection of fire-retardant tapes to help seal the job.
Americover Has You Covered
Americover cares about improving worker safety through the prevention of electrical accidents and fire hazards. We can all make a difference by following best practices, refusing to take short cuts, and watching out for one another on the job site.
OSHA provides a number of critical resources and electrical safety training to educate workers on how to stay safe on the job site. Visit www.osha.gov/SLTC/electrical/training.html to learn more.
Trusted by Growers, Builders, and Distributors
Americover is the smart source for polyethylene and plastic sheeting. Trusted by contractors and distributors across construction and agriculture industries, our American-made products combine reliability with quality and innovation. We protect and enhance projects from the ground up with reliable solutions, responsiveness, and quick turnarounds.
As an Americover customer, you will receive the personalized support of a dedicated account manager to simplify the ordering process and ensure the best solution for every one of your projects. Our friendly, knowledgeable staff is here to answer your questions and fulfill orders Monday-Friday from 6 a.m. to 6:30 p.m. Pacific Standard Time. If you would like to speak with one of our experts, call us at 760-388-6294 or contact us.